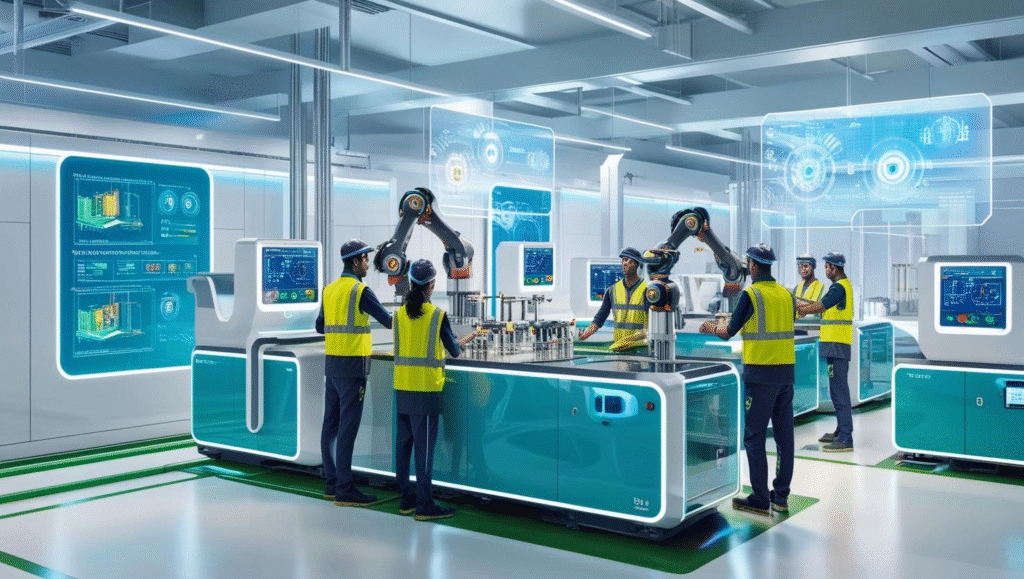
In its quest for a USD 1 trillion valuation by 2025-26, India’s manufacturing sector is turning factories into smart, efficient centers of production through the use of digital twins and predictive maintenance. These Industry 4.0 technologies, being used by 76% of global leading manufacturers, are picking up in India too, improving productivity and reducing expenditure, industry executives claim. From car factories in Pune to textile factories in Coimbatore, the factory of the future is already here, but there are challenges ahead. Digital twins—virtual copies of physical assets—facilitate real-time monitoring and optimization. A Tata Motors factory in Pune employs digital twins to model production lines, cutting downtime by 15%, according to a 2024 CII report. Predictive maintenance fueled by AI and IoT sensors predicts equipment failure before it happens. For example, a Bhubaneswar steel plant saved USD 2 million a year by forecasting furnace problems, reducing disruption. All these technologies combined reduce maintenance expenses by 20-30% and increase production, Invest India points out. In India, adoption is increasing. The automotive industry, which contributes 7% to GDP, applies digital twins to quality control, while Hyderabad-based pharmaceutical companies utilize predictive maintenance to ensure regulatory compliance. The Production Linked Incentive (PLI) scheme with USD 27 billion has incentivized tech upgrades, making it easy for SMEs in centers such as Rajkot to adopt IoT sensors. Cloud subsidies by the Digital India mission further facilitate companies to store and analyze data, making it efficient. But there are obstacles. 60% of MSMEs are discouraged by high setup expenses, without funds for sensors or software, according to a Ficci survey. Just 30% of India’s workforce is AI-IoT trained, dragging out implementation. Data security is another area of concern, with 43% of manufacturers having encountered cyberattacks in 2024. Weak internet connectivity in Tier-2 cities such as Ludhiana also impedes real-time monitoring. Solutions are appearing. The Digital MSME Scheme provides 50% subsidies for cloud and IoT tools, and Skill India trains 10,000 workers every month in digital technologies. Public-private partnerships, such as those in Tamil Nadu’s Oragadam hub, offer shared 5G infrastructure, augmenting connectivity. MSMEs can begin with low-cost sensors, scaling up as profits improve, experts advise. Basic cybersecurity software and training can help reduce risks. The effect is evident. Factories working on digital twins have 15% increased productivity, according to Nasscom, making India a contender with Vietnam and China. With FDI flows reaching USD 17.96 billion in FY23-24, technology-enabled factories entice global companies such as Siemens, which introduced AI solutions during Q2 2025. “Digital twins are game-changers,” declared Priya Menon, who is a CII analyst. “They’re constructing India’s smart factories.”