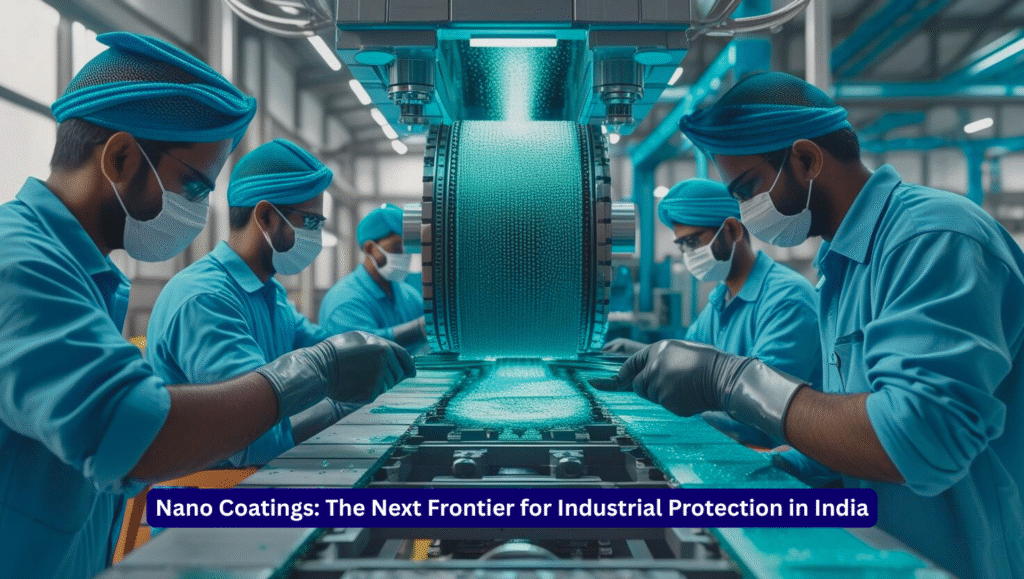
As India’s industrial segment drives towards an anticipated USD 1 trillion contribution to the economy by 2030, the need for high-end protective solutions is skyrocketing.
Nano coatings, utilizing nanotechnology to design ultra-thin, high-performance coatings, are turning out to be a paradigm shift for industrial protection.
Packing more durability, corrosion resistance, and environmentally friendly benefits, these coatings are revolutionizing industries from automotive to marine. High costs and low MSME adoption are proving challenges to generalized deployment.
Nano-coatings, specifically engineered at the nanoscale (1-100 nanometers), create molecular barriers that improve surface characteristics such as hydrophobicity, scratch resistance, and anti-corrosion. The nanocoating market globally, worth USD 10.9 billion in 2024, is anticipated to grow to USD 27.5 billion by 2033 at a CAGR of 10.5%, with Asia-Pacific dominating due to aggressive industrialization.
India, one of the leading players in this geography, is experiencing increasing adoption in the automotive, electronics, and infrastructure space, fueled by the demand for durable, long-term sustainable solutions.
Indian industry leaders are leading this charge. Nanova Care Coat, spearheaded by polymer scientist Dr. Swapan Ghosh, has indigenously developed nano coatings for anti-corrosion (HVAC systems), anti-dust (fan blades), and hydrophobic uses (commercial buildings).
Their products, which are inspired by nature, improve strength and minimize maintenance expenses. Nasiol India’s Smart Silis Tech provides customized coatings for industrial surfaces with corrosion resistance and up to 9H hardness, protecting from scratches and UV exposure.
At Paint India 2024, Arkema introduced waterborne nano coatings with 97% bio-based content, minimizing carbon footprints while ensuring performance in industrial uses.
Key uses are pushing adoption. In the automobile industry, nano ceramic coatings such as Nasiol’s products shield car paint from acid rain and UV radiation and increase surface life by seven years. In construction, Nanoman coatings protect porous materials such as wood and stone, while facilitating breathability, while keeping water and contaminants at bay, suitable for India’s tropical weather.
Corrosion-resistant nano coatings, which include nanoparticles such as silicon carbide (SiC) and zinc oxide (ZnO), provide improved protection in aggressive environments, which is essential for oil and gas pipelines and ships.
A 2024 study revealed SiC-Ni nanocomposite coatings enhanced corrosion resistance by serving as inert barriers, critical for India’s coastal industries. Stimulus-responsive smart coatings, for example, those created by Nanografi, sense changes in pH or humidity and release inhibitors to restore micro-damage, prolonging machinery life in industries such as aerospace.
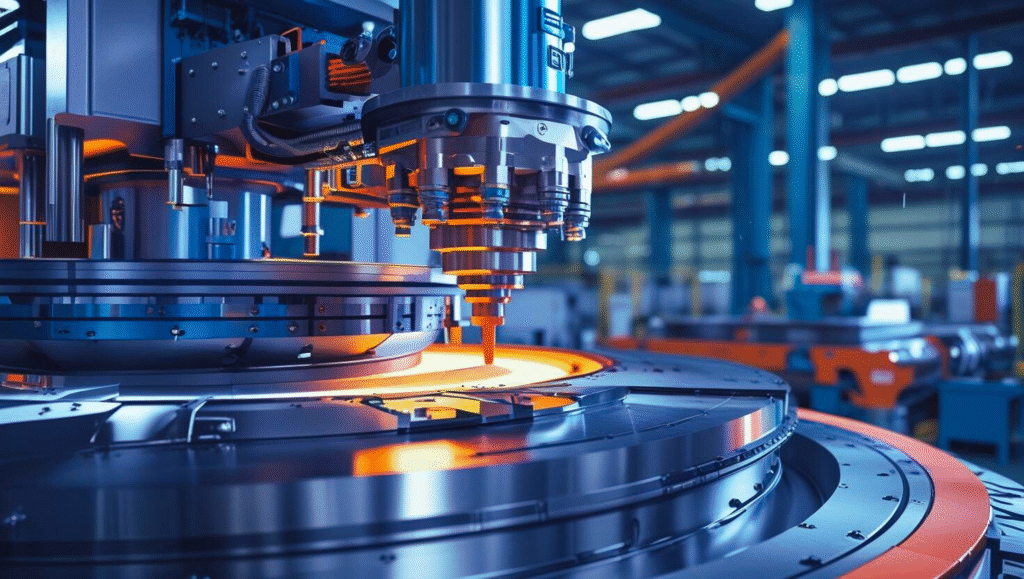
Government patronage is giving a boost to growth. The ‘Make in India’ program and the Production-Linked Incentive (PLI) scheme are incentivizing R&D in new-age materials, with Rs. 50,000 crore for the National Research Foundation (NRF) for industry-academia collaboration.
The MSME-centric Raising and Accelerating MSME Performance (RAMP) scheme is driving technology uptake, allowing smaller businesses to invest in nano coatings.
National Green Mission is consistent with the industry movement towards environmental-friendly coatings, minimizing VOC emissions and use of toxic chemicals such as PFAS, as with Lotus Nano’s PFAS-free technology.
Green growth is a major driver. Waterborne nano coatings, such as ANT LAB’s, provide self-cleaning and UV-blocking functionality for solar panels and concrete, boosting energy efficiency by up to 20% in certain applications.
Bio-based nanomaterials like nanocellulose offer mechanically strong, biodegradable alternatives for anti-corrosion coatings in the construction industry.
A recent 2024 study featured polyurethane (PU) coatings with functionalized Ta3N5/graphene carbon nitride (GCN) with a water contact angle of 165° and corrosion resistance after 45 days of electrolyte exposure, which is promising for use in aerospace.
Despite progress, challenges remain. High costs—often 20-30% more than traditional coatings—limit adoption among MSMEs, which contribute 23% to the paint industry’s market share.
Only 10% of SMEs have adopted nano coatings due to financial constraints, per a 2024 SIDBI report. Skill shortages are a hurdle; just 5% of the workforce is trained in nanotechnology applications, per Nasscom.
Infrastructure problems, such as irregular power supply in Tier 2 cities, hamper manufacturing, with a tweet on X by @IndiaIndustry highlighting Rs. 1-2 lakh worth of monthly outages for SMEs.
Lack of awareness in rural markets and cumbersome regulatory clearances for new formulations hinder progress.
To reduce these obstacles, specialists suggest focused interventions. Subsidies on the Technology Upgradation Scheme can be a cost-off for MSMEs. An extension of vocational training through Skill India with an emphasis on nanotechnology can compensate for skill deficiencies.
Simplifying patent procedures, which now take 4-6 years as against China’s 2 years, would boost innovation.
Public-private collaborations, such as Arkema’s Navi Mumbai R&D facility, can catalyze scalable solutions. Industry association-led awareness campaigns can stimulate demand in Tier-II and Tier-III cities.
Nano coatings are set to revolutionize industrial protection in India, with durability, sustainability, and performance in a rapidly industrializing nation.
Through smart investments and reforms, India can dominate the world’s nanocoating industry, preserving assets as well as the environment. The next horizon is now—if only India grabs it.