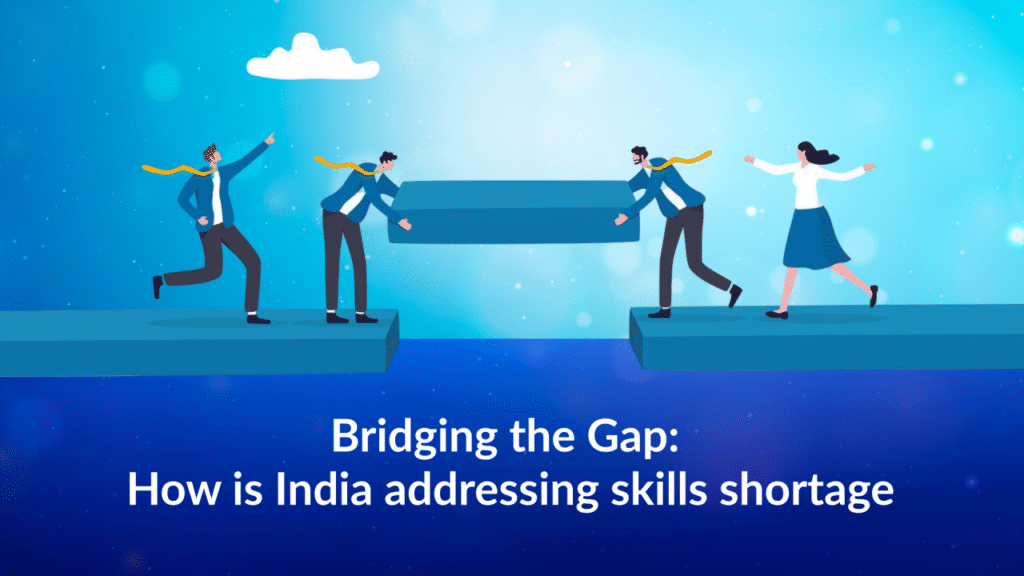
With India seeking to become a global manufacturing hub through the ‘Make in India’ campaign, an acute challenge stands in its way: an impending industrial skills gap threatening to derail economic dreams.
With merely 10% of the workforce being Industry 4.0 technology-trained in automation and AI, a 2024 Nasscom report states, the manufacturing industry in India lacks skilled workers. Vocational training is becoming a prime solution to fill this vacuum, imparting millions with the skills necessary to fuel industrial expansion.
However, systemic issues need to be resolved to make these programs effective.
India’s industrial economy, contributing 17% to India’s GDP, is based largely on Micro, Small, and Medium Enterprises (MSMEs), which have more than 111 million employees and generate 45% of manufacturing production.
Yet, quick change in technology in industries such as electronics, automobiles, and pharma requires robotic skills, IoT expertise, and data analysis skills, which India lacks. According to a World Economic Forum report of 2024, an estimated 50% of India’s workforce will require reskilling by 2030 to align with industry needs, with manufacturing lacking 2 million skilled workers every year.
Vocational training courses are rising to the challenge. The Skill India Mission, which was initiated in 2015, plans to skill 400 million workers by the year 2030, including 15 million workers by 2024, according to the Ministry of Skill Development and Entrepreneurship (MSDE).
The Pradhan Mantri Kaushal Vikas Yojana (PMKVY) has skilled 10 million youth with industry-aligned skills in areas such as textiles and logistics.
In Tamil Nadu, automotive clusters collaborate with Industrial Training Institutes (ITIs) to provide EV manufacturing courses, increasing employability by 30%, according to a 2023 MSDE study.
Public-private partnerships are scaling up impact. Players such as Siemens partner with ITIs to deliver dual training programs, which combine classroom studies with on-the-job training. In Maharashtra, Tata STRIVE has trained 50,000 youth since 2016, of whom 70% found employment in manufacturing.
Firms are encouraged to employ apprentices under the National Apprenticeship Promotion Scheme (NAPS) with 1.5 million apprentices placed in 2024, according to MSDE statistics. Cluster-based programs, such as Surat’s diamond trade, provide common training centers to cut costs for MSMEs and facilitate skills such as precision cutting.
Online platforms are redefining access. The Skill India Digital Hub, established in 2023, has taught AI, robotics, and supply chain management through online courses that have already reached 2 million learners by 2024.
Collaborations with technology companies such as Microsoft and Google have made digital tools training affordable for MSMEs, which is essential for e-commerce and automation. In Karnataka, women-owned MSMEs in the apparel industry have leveraged these platforms to reskill 10,000 workers, enhancing productivity by 20%, according to a 2024 CII report.
In spite of advancements, hurdles remain. India has a mere 5% of its workforce with formal vocational training, in contrast to 68% in Germany, according to a 2023 ILO report. Rural regions, where 70% of MSMEs are located, lack ready access to training institutions and high-speed internet to support online learning.
The irregular power supply in Uttar Pradesh affects training centers, impacting 30% of ITI programs. Quality is highly variable, with most ITIs adopting old curricula that do not meet Industry 4.0 demands.
Finance is also a constraint; the 2024-25 skill development outlay of Rs. 15,000 crore will not be enough to upskill 400 million workers.
Gender imbalances persist. Women, constituting 20% of MSME employees, are but 15% of vocational apprentices, according to MSDE statistics. Social stigma and ignorance discourage participation, especially in rural regions. Coordination among states and the central government is also uneven, with developed states such as Tamil Nadu leaving Bihar behind in terms of training infrastructure.
Competition from the global platform mounts—ASEAN countries such as Vietnam provide a more skilled labor force at lower prices, siphoning off FDI from India.
To close the gap in skills, experts recommend a multifaceted strategy. Curricula aligned with industry requirements, such as the Automotive Skill Development Council’s EV skilling modules, are essential. Augmentation of digital infrastructure, such as the rollout of 5G across rural India, can increase access to online training.
SCALE can be boosted through increased funding, including the use of public-private partnerships and incentives such as tax relief for companies making investments in skilling.
Programs like the Women Entrepreneurship Platform (WEP) must be scaled up to increase the participation of women.
Strengthening of apprenticeship training, with live industry exposure, can enhance employability, evident from Germany’s dual training model.
Vocational training is India’s key to a trained industrial workforce, critical for reaching $2 trillion exports by 2030. By solving funding, quality, and access issues, India can enable its 63 million MSMEs and large enterprises to compete on the world stage. As the country drives towards Viksit Bharat@2047, investing in skills today will determine industrial success tomorrow—if the ecosystem is up to it.