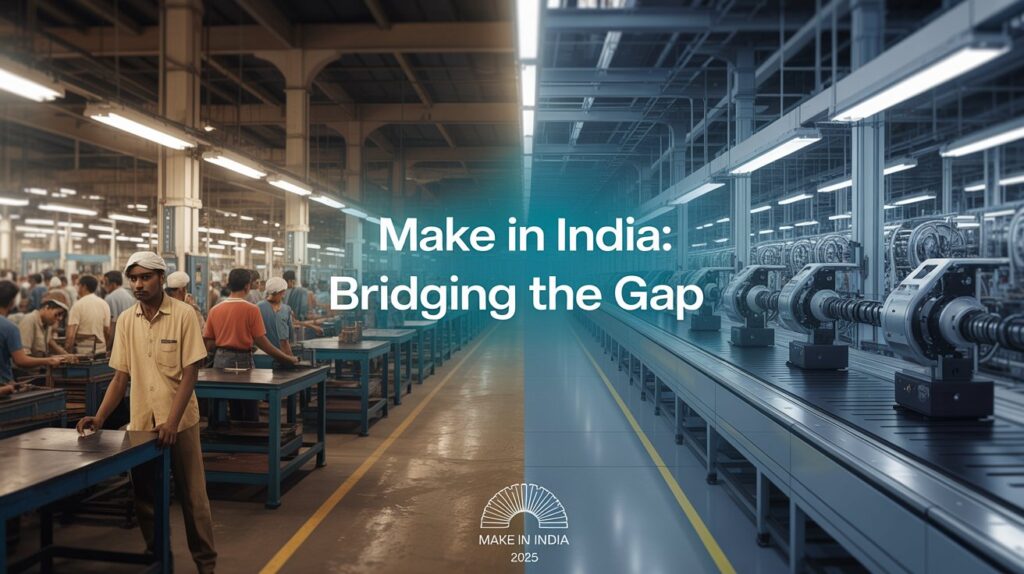
It was September 2014 when the ‘Make in India’ campaign was kicked off with a vision to make India a global manufacturing hub, hoping for 25% of GDP from manufacturing by 2025, from 16%.
As the campaign reaches its decade milestone, India’s industrial output has made substantial leaps, but the difference between aspirations and realities on the ground is acutely apparent.
With foreign investment rushing in and reforms re-fashioning the industry, is ‘Make in India’ living up to its promise, or are structural issues keeping it back?
The vision of the initiative was ambitious: increase manufacturing, create 100 million jobs, and drive India’s global competitiveness.
Backed by the likes of the Production-Linked Incentive (PLI) scheme, with $27 billion for 14 sectors, and the National Infrastructure Pipeline (NIP), with $1.8 trillion for 7,500 projects, ‘Make in India’ has made concrete headway.
The electronics industry, especially mobile phone manufacturing, is a prime example of success. Today, 97% of Indian smartphones are being locally manufactured, with Apple relocating iPhone manufacturing to plants in Tamil Nadu and Karnataka.
In 2024, exports of electronics jumped to $29 billion, a 23% year-on-year growth, according to the Ministry of Commerce.
Pharmaceuticals and chemicals also show the upward trend. India, the third-largest pharma manufacturer globally by volume, is providing 62% of the world’s vaccines and has been decreasing dependence on Chinese APIs through domestic production spurred by PLI.
The chemical industry is expected to grow to $160 billion by 2025 with a CAGR of 7-8%, driven by increasing exports to the EU and U.S.
The automotive sector, covered by the Automotive Mission Plan 2016-26, is expanding, with EV manufacturing picking up steam through auto majors such as Tata Motors and schemes such as the Faster Adoption and Manufacturing of Electric Vehicles (FAME) initiative.
Foreign direct investment (FDI) has been a silver lining. FDI inflows between 2014 and 2024 stood at $667.4 billion, with 2023-24 itself accounting for $44.4 billion, as per DPIIT.
Singapore, the U.S., and Japan are the top investors, with investments such as Foxconn’s $1 billion Gujarat chip factory and Walmart’s $3.5 billion Flipkart investment reflecting confidence.
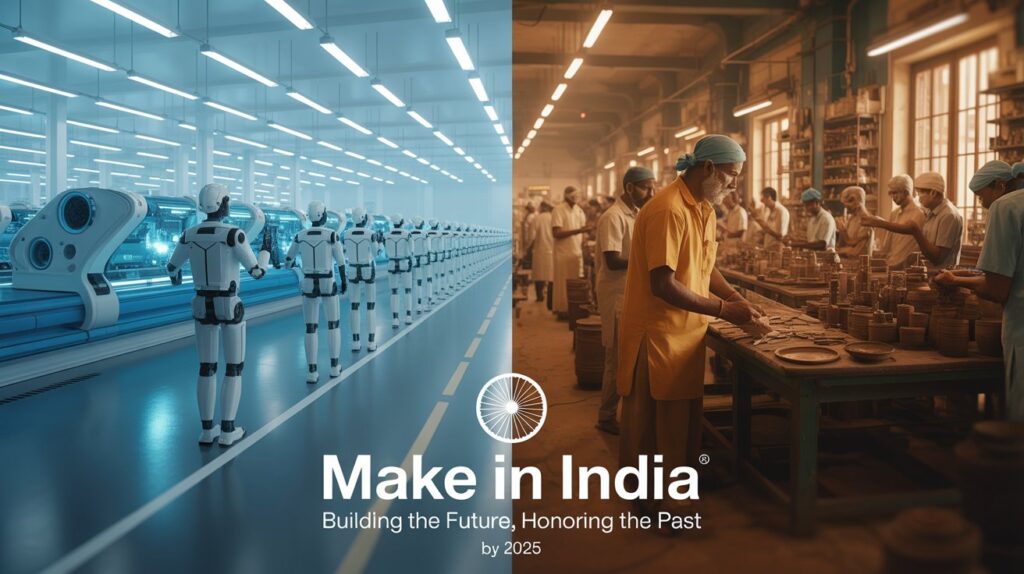
The ‘China Plus One’ approach, fueled by supply chain diversification on a global scale, has made India a sought-after substitute, particularly in electronics and textiles.
Policy and infrastructural reforms have supported the march ahead. National Logistics Policy (NLP) seeks to lower the cost of logistics from 13-14% to 9-10% of GDP by 2027, while PM Gati Shakti unifies 16 ministries to rationalize connectivity.
The establishment of 100 plug-and-play industrial parks, outlined in the Union Budget 2024-25, eases establishment for manufacturers. Free Trade Agreements (FTAs) with Australia and the UAE, and ongoing negotiations with the EU, are increasing access to markets.
However, the reality lags behind expectations. The manufacturing’s percentage of GDP still stands at 17%, falling woefully short of the desired 25%. The creation of employment has been small, with just 60 million jobs created as of 2024, according to the International Labour Organization, far from the desired 100 million.
While MSMEs account for 45% of manufacturing output, they suffer from high compliance burdens and restricted credit availability, even with programs like the Credit Guarantee Fund Trust for Micro and Small Enterprises (CGTMSE).
According to a 2023 report by Confederation of Indian Industry (CII), bureaucratic tardiness and cumbersome land acquisition hinder investors, especially in Tier 2 cities.
Infrastructure gaps remain. Last-mile connectivity and unreliable power supply raise costs of operations, with logistics costs in India still twice that of developed economies.
India is placed 62 in the Ease of Doing Business Index by the World Bank, behind competitors such as Vietnam. Skill gaps are a key bottleneck—only 10% of the workforce is Industry 4.0-skilled in technologies such as automation and AI, according to a 2024 Nasscom report.
Environmental issues such as pollution caused by industrial clusters also jeopardize India’s convergence to global ESG norms.
The focus of the initiative on big industries has occasionally eclipsed MSMEs that employ 111 million workers.
Cluster-based schemes benefit MSMEs, but irregular implementation among states means that states such as Bihar and Uttar Pradesh fall behind. An X post by @EconObserverIndia lamented the slowness with which regulatory simplification has been happening, pointing out that 30% of MSMEs continue to suffer delays in approvals.
Global competition, especially from ASEAN countries with lower import tariffs, also adds pressure on India’s export aspirations.
India requires targeted reforms to fill the gap.
Streamlining regulations via the National Single Window System, widening skill development under the Skill India Mission, and green technology investments such as solar-powered production have the potential to raise competitiveness. MSME support needs to be strengthened with easy availability of credit and adoption of technology.
According to Commerce Minister Piyush Goyal, reaching $2 trillion worth of exports by 2030 would involve a “whole-of-government” strategy in overcoming structural challenges.
‘Make in India’ has set the stage strongly, making India a manufacturing player.
However, the ambitious 2014 goals of 25% GDP contribution and 100 million jobs elude us today. Strategically executing, India can bridge this gap, capitalizing on its demographic dividend and changes in global supply chains to be a manufacturing hub.
The way forward requires focus, flexibility, and inclusivity to make dreams a reality.