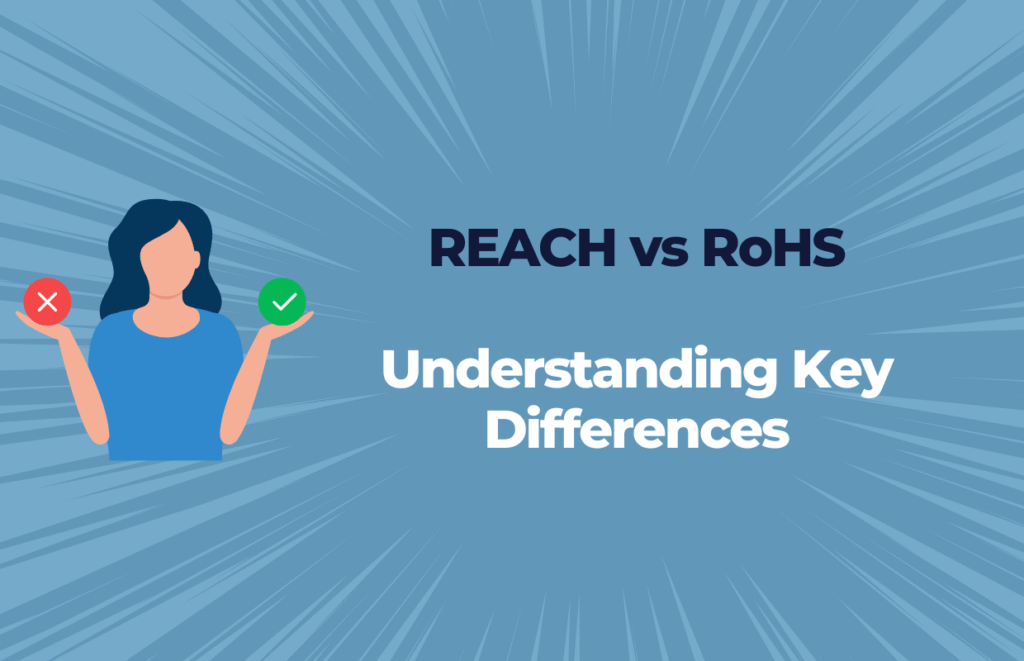
As environmental and health issues globally continue to escalate, world-wide regulations such as REACH, RoHS, and green chemistry concepts are transforming the adhesives market towards low-VOC, non-toxic, and safer formulations.
With India’s USD 2.1 billion adhesives market in 2024 and expected 6.5% CAGR until 2030 under growing scrutiny, these standards are forcing innovation at the expense of manufacturers needing to walk the tightrope of compliance, performance, and price.
With mounting regulatory pressure, Indian manufacturers of adhesives are conforming but high prices and technical challenges are in danger of impeding progress, especially among small players.
REACH (Registration, Evaluation, Authorisation, and Restriction of Chemicals) is the regulation of the European Union, under which more than 23,000 chemical substances are controlled and makers are made to evaluate and reveal risks. It limits dangerous chemicals such as formaldehyde and toluene, used in urea-formaldehyde adhesives widely employed in India’s plywood and building industries, utilizing 30% of adhesives.
RoHS (Restriction of Hazardous Substances), also EU-led, restricts substances such as lead and cadmium in adhesives used in electronics, vital as India’s electronics industry expands by 15% every year.
Green chemistry principles with a focus on non-toxic and sustainable raw materials also encourage biodegradable and bio-based adhesives, following India’s National Green Mission and international ESG standards.
Such regulations are changing adhesive formulations. Low-VOC adhesives, cutting emissions by as much as 80%, are sought because of REACH’s VOC restrictions and India’s Bureau of Indian Standards (BIS) regulations.
Water-based, non-toxic adhesives, such as those Pidilite has developed for packaging, remove formaldehyde, complying with REACH’s no-added-formaldehyde (NAF) standards.
It was reported in 2024 by CII that 65% of Indian manufacturers are moving to water-based or bio-based adhesives to meet these standards, as export markets such as the EU, which represent 20% of India’s adhesive exports, lead the charge. Consumer demand, with 60% of urban Indians requiring green products according to a 2023 Nielsen survey, increases this trend.
Performance gaps are being filled by innovations. Soy adhesives, applied in furniture production, have low-VOC bonding with 6.4-MPa shear strengths when cross-linked by urea-formaldehyde, according to a 2019 study. Lignin-based adhesives, sourced from India’s 20 million-ton pulp industry, have 80% of phenol-formaldehyde’s tensile strength, according to a 2024 study, and comply with REACH due to biodegradability. Casein-based adhesives, made by companies such as Specialty Organics, provide non-toxic woodworking bonding, with modified formulations that contain phosphorus enhancing water resistance.
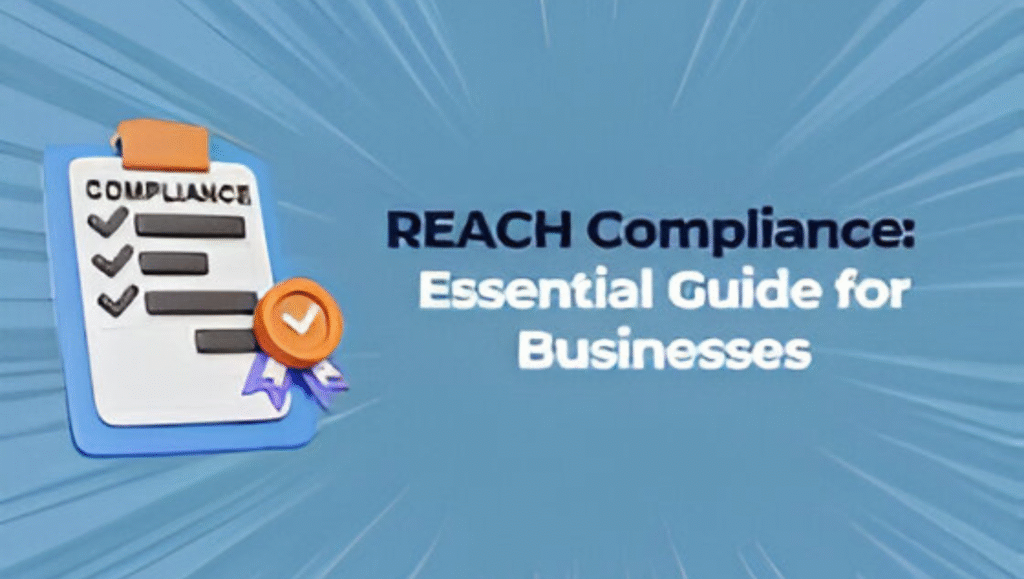
Nanocellulose reinforcement, taken up by companies such as Henkel India, enhances adhesive strength by 15% while satisfying green chemistry’s sustainability requirements, enabling applications in India’s burgeoning EV and packaging markets.
Manufacturers have major stakes in global regulations. Adhering to them guarantees access to high-value markets such as the EU and U.S., which have stringent import requirements. For example, RoHS compliance is paramount for India’s exports of electronics adhesives, estimated to grow to USD 500 million by 2030.
Non-compliance can lead to fines, product bans, and reputational loss, as in 2022 when some Indian adhesive shipments were rejected in Europe due to high formaldehyde content. In 2024, a Deloitte study estimated that compliance with REACH increases 10-15% of production costs, but 20% of export revenues for compliant companies.
Green chemistry lowers long-term expenses by conserving energy and minimizing waste, with water-based adhesives reducing production emissions by 25%.
Indian industry is acting positively. Asian Paints has made investments in R&D for low-VOC, REACH-compliant adhesives for construction, and Kansai Nerolac’s automotive applications waterborne adhesives comply with RoHS requirements. MSMEs, which account for 40% of Indian adhesives, are helped by the Raising and Accelerating MSME Performance (RAMP) scheme, which assists technology adoption.
The Production-Linked Incentive (MSME) scheme encourages R&D of sustainable formulations, with Rs. 50,000 crore being provided to the National Research Foundation for industry-academia partnerships.
The Skill India Scheme has also trained workers in advanced manufacturing, including green chemistry applications.
Even with progress, there are challenges. Compliance costs, 20-30% more than traditional formulations, burden MSMEs, with only 15% of them embracing these technologies, according to a 2024 SIDBI report.
Skill gaps, with only 5% of employees trained in nanotechnology or adhesive use, according to Nasscom, keep innovation back.
Infrastructure shortcomings, such as the erratic power supply in rural India, interrupt production, which results in heavy monthly losses for small businesses, according to industry reports. Regulation slows progress.
ASEAN countries’ global competition with lower priced substitutes brings additional pressure.
To manage such challenges, experts suggest strategic interventions. Subsidies can mitigate cost for MSMEs.
Developing training through initiatives like Skill India can mitigate skill gaps. Developing infrastructure, as envisaged under government schemes, will enable production.
Collaboration with educational institutions can spur research into compliant, cost-friendly formulations. Industry association-led awareness campaigns can increase demand in smaller markets.
International norms are guiding India’s adhesives sector towards safer, more environmentally friendly products, following regulations and staying competitive.
With a USD 3 billion market in the making, Indian manufacturers can take the lead in low-VOC and non-toxic adhesives.
Meeting global benchmarks by overcoming cost, capability, and infrastructure hurdles, India can achieve a greener future while propelling innovation.